The ratio of a pneumatic lubrication pump is determined by the relationship in size between the air motor piston and the fluid piston. For example, on a 5:1 ratio oil pump, the fluid piston is five times larger, in effective area, than the fluid piston. What does this mean in practical terms? It means that for every 1 psi of air pressure that you put to the pump, you get 5 psi of fluid pressure. So, on a 5:1 ratio pump, operating at 100 psi of air pressure (based on the gauge of the air regulator on the pump), you will have 500 psi of fluid pressure at the pump outlet. This fluid pressure figure is at the pump outlet only. I can calculate friction line loss, based on the length and ID of the piping you plan to incorporate. Give us a call and we will properly size a pump for you.
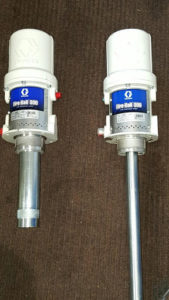
A 5:1 ratio oil pump on left, and a 50:1 ratio grease pump on right. Identical air motor but note the size differential on the suction tubes.
A 5:1 ratio oil pump on left, and a 50:1 ratio grease pump on right. Identical air motor, but note the size differential on the suction tubes.
The ratio and type of pump that is appropriate for the material that you intend to pump, are dependent on the characteristics of that material. We discussed ratio above. By type of pump, I mean double ball versus priming piston or, as they are sometimes referred to “Shovel” pumps. A shovel pump is necessary to pump automotive grease, and materials with similar viscosity (NLGI #2 grease-200,000 to 250,000 Centipoise) because these materials are resistant to flow. The shovel physically lifts the material into the pump suction tube. With double ball pumps, the action of the fluid piston creates a vacuum in the suction tube, and atmospheric pressure (14.7 psi/si) pushes the material into the pump tube. You can see then that a material that is resistant to flow, can’t be pumped with a double ball pump.
Typically (but not always) shovel pumps are available in higher ratios, such as 50:1. With a 50:1 ratio pump, for every 1 psi of air pressure, you will get 50 psi of fluid pressure (or semi solid, as it were) at the pump outlet. At 150 psi air pressure (we often operate grease pumps at full line air pressure, and this is fine) you will get 7500 psi of grease pressure. This high pressure is necessary to move the thick material, especially if it is a plumbed system, and still have adequate pressure to open a zirc fitting.
A quick and easy method that can be used to determine if you require a shovel type pump is to open your material container and scoop out a small quantity of the material using a Solo cup, a measuring cup, your gloved hand, etc. Then, watch what the material does. If it quickly flows in, making the scooped out area invisible, you can get by with a double ball pump. If the scooped out area doesn’t fill in, you need a shovel pump.
There is no hard and fast rule relative to setting the air pressure on a pneumatic pump. The best method is to go to your furthest dispense point (on a multi point system or your one and only dispense point on a single point system) and slowly turn up air pressure until you get a suitable pressure and flow rate, without a lot of splashing due to excessive pressure.
Automotive grease is available in three sizes of bulk containers-a five gallon pail, which is commonly referred to as a “35lbs pail”, a 16 gallon drum, commonly referred to as a “120lbs” drum, and a 55 gallon drum, commonly referred to as a “400lbs” drum. Specify one of these sizes when ordering grease and grease pumps.
With lubrication equipment, like virtually everything out there, you get what you pay for. If you buy cheap, you get short life and recurrent service issues. Buy the product of an American company, like Lincoln for the best value.
We repair all brands and types of lubrication equipment. Pumps, reels, meters, whatever. Send it to us and we’ll get you a written estimate and lead time within a day or two.
If you need a lubricant inventory control system (think Graco Matrix) or an automated, repeatable production line system, give us a call. We are experts in this field.